- Home
- Blog
- Mineral Solution
- Mastering Magnetic Separation Method: Unlocking Power
- mmldigi
- Published:
- Updated: January 10, 2025
Preface
Magnetic separation is widely used in many industries as it aids in the separation of iron ore and other materials. This method uses the magnetic field to attract the magnetic particles, and is thus appropriate for large volumes of slurry. It is especially useful in large scale operations since it efficiently isolates the mineral of interest from the other non-magnetic materials. This technique is applied due to its simplicity, efficiency, and high capacity for flow rates and volumes of waste, which is why it is essential in mining, recycling, and other industries. This blog will give an overview of the scientific principles of magnetic separation, describe how magnetic separation works, the factors affecting it and the different magnetic separation equipment to help you choose the right magnetic separation equipment for your process.
Understanding Magnetic Separation Method
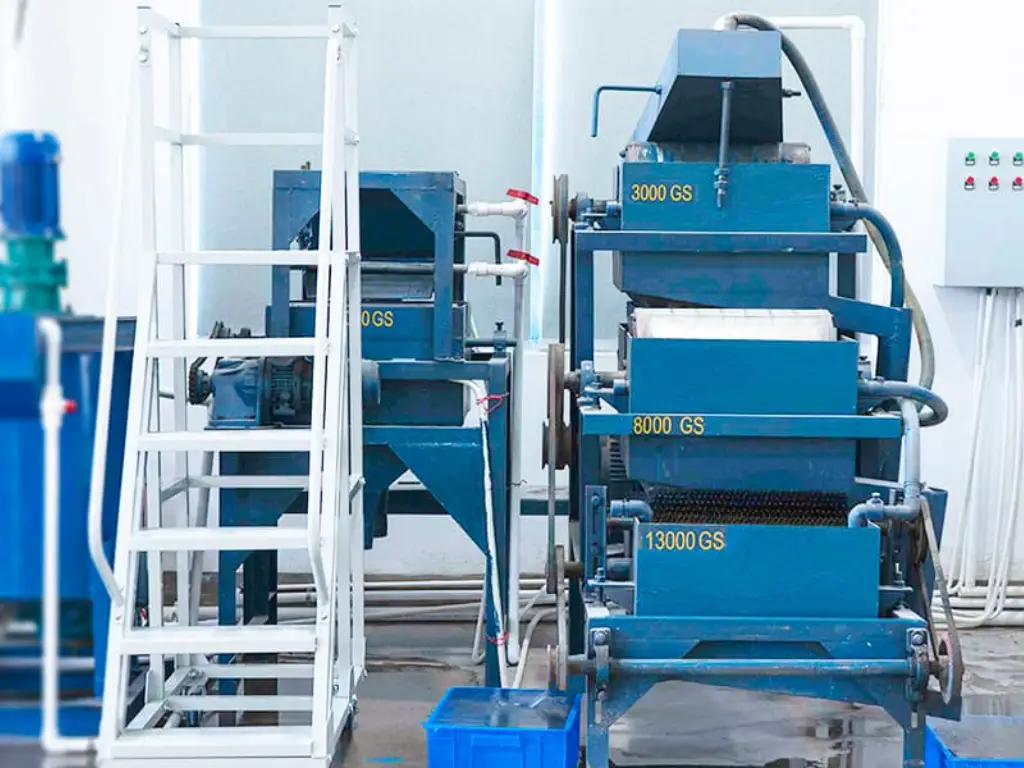
The magnetic separation method is one of the most effective and easiest methods of getting the iron ore from the other materials. This technique is very useful in high throughput operations where large volumes of slurry are processed in order to separate the iron ore from the non-magnetic materials. The method employs an applied magnetic field to reorientate the long axes of the magnetic particles to improve the separation process. Also, it can handle high flow rates and high volumes of process waste residuals that are ideal for large-scale industries, especially in areas such as Europe. Due to the simplicity and efficiency of this method, it is widely used in many industries, providing an opportunity to extract valuable minerals.
Electromagnetic System vs Permanent Magnetic System
When it comes to magnetic separation, there are two primary systems in use: electromagnetic and permanent magnetic systems. Each has its unique characteristics, advantages, and applications.
Feature | Electromagnetic System | Permanent Magnetic System |
---|---|---|
Magnetic Field Generation | Generated by passing electric current through coils. Adjustable magnetic field strength. | Utilizes permanent magnets to create a constant magnetic field. Fixed magnetic field strength. |
Energy Consumption | Requires continuous electrical power to maintain the magnetic field. Higher operational costs. | No energy consumption for maintaining the magnetic field. More energy-efficient and cost-effective. |
Maintenance | Higher maintenance due to electrical components. Needs regular inspection and replacement of worn parts. | Low maintenance as there are no electrical components. Long-lasting with minimal upkeep. |
Applications | Ideal for applications requiring variable magnetic field strength, such as fine particle separation and high-intensity processes. | Suitable for applications with consistent separation requirements, such as bulk material handling and recycling. |
Choosing between these two systems depends on specific application needs, including the desired magnetic field strength, operational costs, and maintenance considerations.
Magnetic Separation Examples
Magnetic separation finds application across various industries, offering efficient and effective solutions for material separation. Here are some examples:
● Mining Industry (e.g., Iron ore separation, Extraction of magnetic minerals, Removal of ferrous metals from non-magnetic ores)
Enhance your mining processes by implementing Magnetic Separation in Mineral Processing for superior mineral extraction efficiency.
● Recycling Industry (e.g., Sorting of ferrous and non-ferrous metals, Recovery of metal from waste, Removal of metal contaminants from recycled materials)
● Food Processing (e.g., Elimination of metal impurities from food products, Ensuring product safety and purity Protecting processing equipment from damage)
● Pharmaceuticals (e.g., Removal of metal contaminants from raw materials,Ensuring high purity standards in drug manufacturing, Protecting sensitive equipment from magnetic interference)
Factors Affecting Magnetic Separator Performance
Several factors can influence the performance of a magnetic separator, impacting its efficiency and effectiveness.
● Magnetic Field Strength: The intensity of the magnetic field is very important in the sense that it determines how well the separator will be able to attract and retain the magnetic particles. The degree of separation is also improved by higher magnetic field strengths, particularly for fine particles.
● Particle Size and Distribution: The size and distribution of particles being separated are also other factors that influence the process. Particles that are smaller are usually harder to separate and may need higher magnetic fields or different types of separators.
● Flow Rate and Velocity: The rate and velocity of the material flow through the magnetic separator also determine the efficiency of the separation. The flow rates should be optimal to allow for the best separation without overloading the separator.
● Material Composition: The nature of the material being processed, that is the proportion of magnetic and non-magnetic particles affects the performance of the separator. Some changes may be required depending on the characteristics of the material used.
Magnetic Separator Working Principle
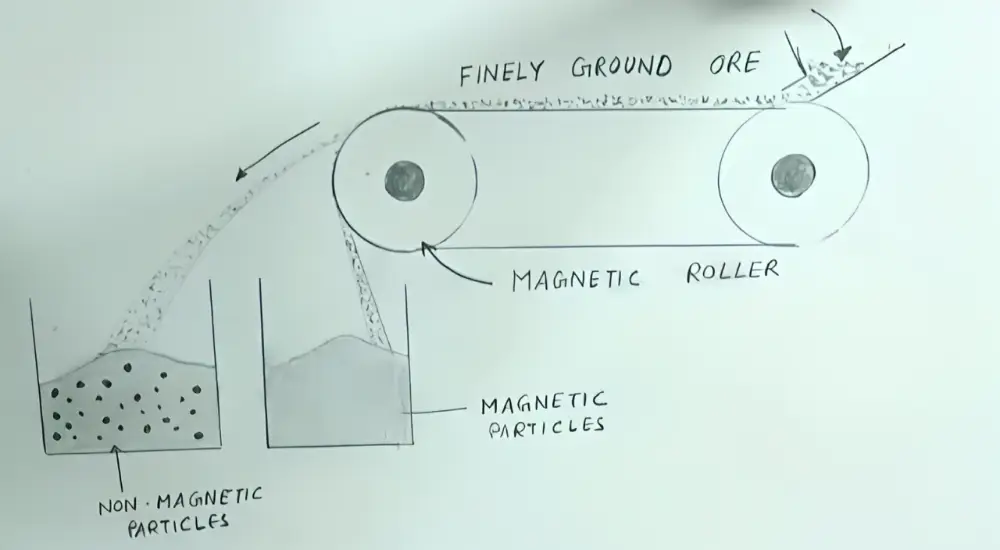
According to the magnetic separator diagram, the working principle is as follows:
1. Feeding Finely Ground Ore
First, the ore is crushed into a fine powder and then the powder containing particles like magnetite, copper, and ilmenite is placed on a conveyor belt. As illustrated in the magnetic separation diagram, this step ensures that the ore is properly spread out, creating an even basis for the separation process.
This first phase is important in order to guarantee that the ore is properly spread out in order to facilitate the separation process. The material can include heavy metal ions and other magnetic impurities. This step creates a basis for the subsequent separation process with the help of a magnetic roller. The magnetic separator is easy to operate, which makes it applicable in various processes of waste disposal.
2. Attraction to Magnetic Roller
When the ore is being transported on the conveyor belt, it comes across a magnetic roller. As shown in the magnetic separation diagram, the external magnetic force developed by the roller pulls magnetic particles such as magnetic seed particles and very soft magnetizable wire matrix to its surface. The non-magnetic particles like silica remain on the conveyor belt and continue to move forward. This stage is useful in making distinctions between magnetic and non magnetic substances. The process utilizes magnetism in order to achieve high adsorption capacity and selectivity in the separation process.
3. Sorting of Magnetic and Non-Magnetic Materials
The magnetic roller rotates to move the magnetic particles to a different path than the non-magnetic particles. Because of the flow velocity and the rotation of the roller, magnetic particles are deviated from the main stream of ore This increases the p removal efficiency and guarantees that magnetic impurities are well separated. The process can process large amounts of ore, which makes it suitable for large scale production.
4. Collection of Magnetic Particles
When the magnetic particles get to the target site, they are then dropped into a receptacle. This is because the magnetic force is reduced enabling these particles to fall off the roller. This stage makes sure that all the magnetic carrier materials are retrieved in the most effective manner. It is a continuous process and can handle high throughput rates, which is ideal for large bales of ore material. The collection is intended for handling of materials like Fe, copper and other magnetic contaminants.
5. Disposal and Waste Treatment
The non-magnetic particles which do not get attracted to the roller further move along the conveyor and are dumped in another container. This final step helps in making a clear separation between the magnetic and non-magnetic materials, which is very beneficial in the management of waste. This structured approach helps in ensuring that the magnetic separator works effectively in separating the materials by the use of magnetism.
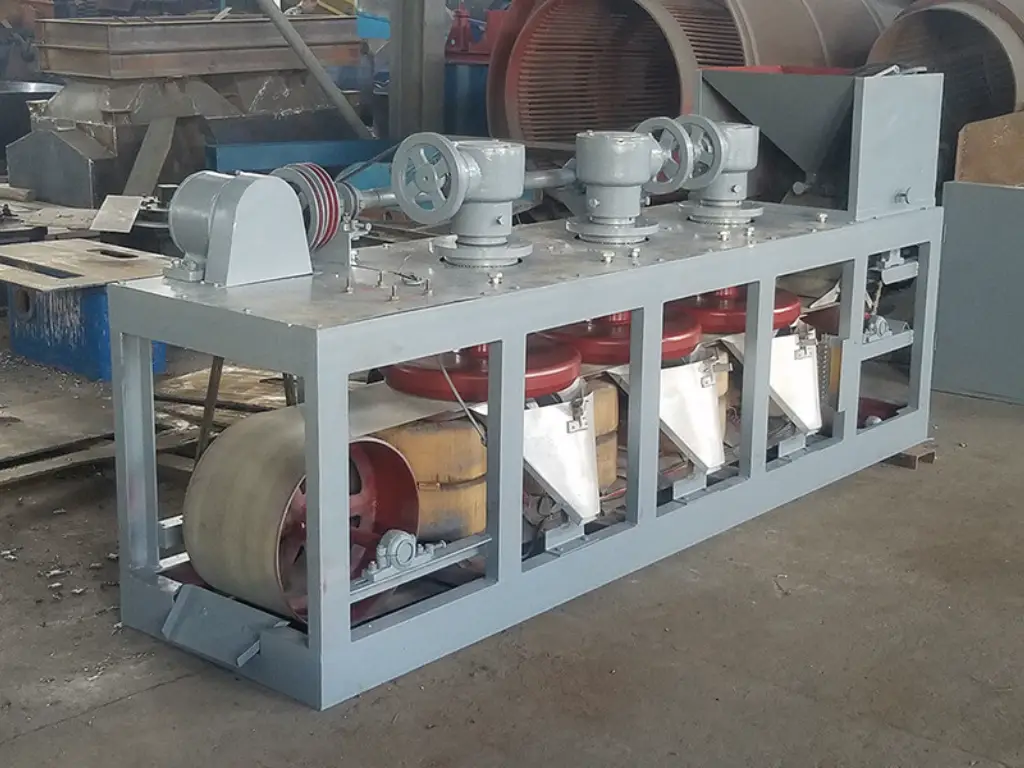
1. Wet Drum Magnetic Separators
These separators are used for the continuous separation of magnetic particles from slurries. They are mostly employed in the mining industry for the separation of iron ore. Wet drum design is especially suitable for large volumes of slurry making it efficient. The structure usually consists of a rotating drum with a magnetic media shell; the latter is usually made of stainless steel. The magnetic field can be produced by permanent magnets or an electromagnet.
Wet drum magnetic separators are very effective in the separation of fine magnetic particles from the non-magnetic material. They have some benefits like easy to maintain and does not require much water and this is very important in areas where there is a shortage of water. But they need to be maintained often to avoid problems such as clogging and wear, which may reduce efficiency. The drums are often made of materials that can handle the abrasive environment of mineral processing such as stainless steel or rubber.
Three disc dry magnetic separators are useful in the separation of fine magnetic particles from dry materials. These separators use three rotating magnetic discs, each of which produces different levels of magnetic fields. This makes it easy to sort materials depending on their magnetic characteristics as they are easily separated. The equipment is used in mineral processing to separate non-magnetic minerals from magnetic ones, for instance in the processing of tin, tungsten and other related minerals. The major parts are the feed hopper, magnetic discs and the conveyors, which are mostly made of stainless steel for strength.
These separators are especially useful for small scale operations because they can handle small particles at low rates of throughput. The feature of multiple discs enables a high selectivity and accuracy in the separation process which is very important when dealing with valuable minerals. However, they have lower capacities and hence are not ideal for large scale industrial uses. Some of the factors that may affect the performance of the equipment include feed particle size and the moisture content of the material being fed to the equipment.
Electrostatic separators use an electric field to sort particles according to their electrical conductivity. They are especially applied in the process of separating non-magnetic materials from magnetic ones and are normally used in combination with magnetic separators. These separators are very effective particularly in the separation of fine particles and materials that have close physical characteristics. The main parts are the corona electrode, the grounded electrode, and a high voltage power supply. The materials used are usually able to withstand the tough working environment due to their corrosion resistance.
The efficiency of electrostatic separators depends on the working conditions such as humidity, temperature, and size of the particles. They provide high efficiency in the separation of conductive and non-conductive materials, so they are used in recycling, mineral processing, and even in the food industry. However, the level of control needed for the best performance can be somewhat difficult to achieve and the equipment is not recommended for use with moist materials. Also, safety measures must be put in place to cater for the high voltage that is needed for the operation of the equipment.
High intensity magnetic separators are used to create very strong magnetic fields which are suitable for the separation of weakly magnetic materials. These separators are useful in industries where there is need to separate particles of small size such as in the recovery of hematite and other weakly magnetic particles. The equipment commonly includes a magnetic drum or roll, which is constructed from rare earth magnets, which are much more powerful than ordinary magnets. The construction may also incorporate stainless steel parts due to the high levels of stress that mineral processing entails.
These separators are very efficient in the classification of fine particles to enable the recovery of valuable minerals. But they are energy consuming and need a sound infrastructure to sustain the high magnetic fields. This makes them more appropriate for bigger and more industrial type of businesses. The high cost of rare earth magnets and the energy consumption are the main drawbacks but their ability to separate even weakly magnetic materials often makes the investment worthwhile.
5. High Gradient Magnetic Separators
High gradient magnetic separators (HGMS) employ a matrix of very fine, magnetisable wires to produce a high gradient magnetic field. This kind of setup is especially suitable for the classification of fine and ultrafine particles, which is widely applied in the processes of purifying kaolin, extracting rare earth elements, and eliminating impurities in minerals. The components usually consist of a solenoid coil that produces the magnetic field and a matrix, which is usually made of steel wool or expanded metal to increase the gradient of the magnetic field.
HGMS are characterized by high efficiency and selectivity in the separation of fine particles and are used in mining and paper industries. They are especially useful when it is necessary to separate very fine magnetic particles which cannot be separated otherwise. But they are not easy to manage and control, and need constant supervision and tuning up to ensure their efficiency. The efficiency of the equipment is also influenced by the feed’s magnetic characteristics and particle size.
To explore leading manufacturers of high-performance magnetic separators, click Boost Production: Top 6 Magnetic Separator Manufacturers for detailed information.
How to Choose Magnetic Separators for Different Minerals?
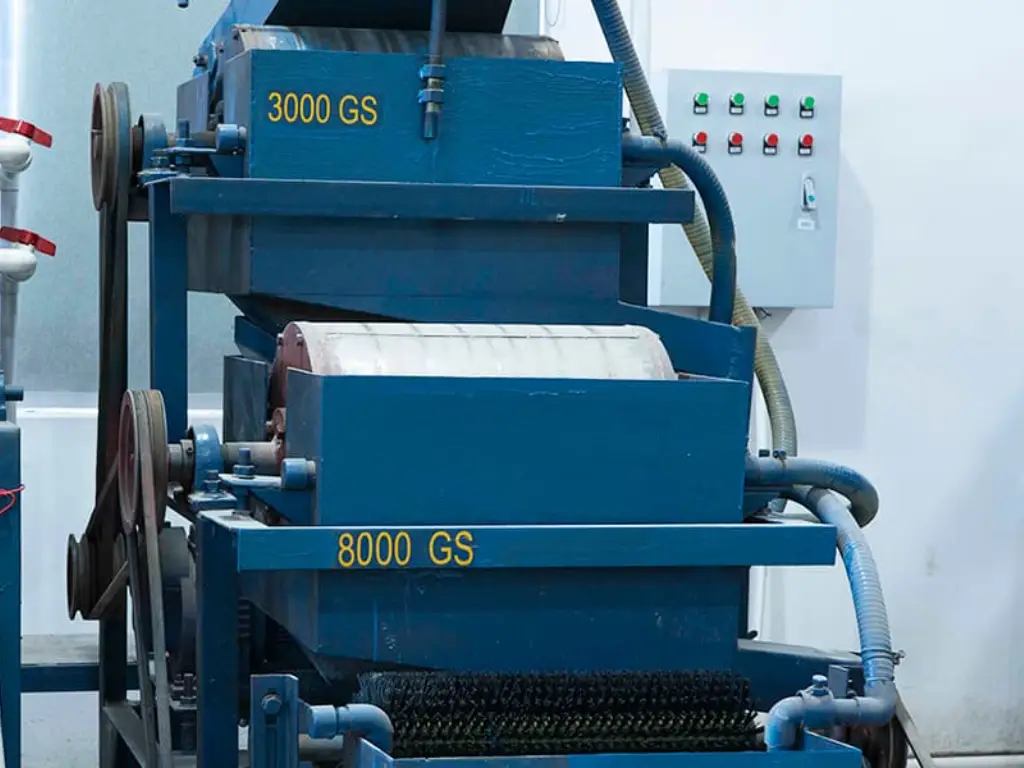
Selecting the right magnetic separator for specific minerals involves several considerations:
● Magnetic Properties of the Mineral: It is important to know the magnetic susceptibility of the mineral. Minerals with high magnetic susceptibility can be separated using normal magnetic separators while those with low susceptibility may need high intensity or high gradient separators.
● Particle Size and Distribution: The size and distribution of the mineral particles are used to determine the type of separator to be used. Ultrafine particles may need more advanced separators with higher magnetic field or better control of the magnetic field.
● Material Throughput and Flow Rate: The type of separator depends on the amount of material to be separated and the rate at which it is required. Large scale separators are required for large scale operations while fine separators may be required for fine operations.
● Operating Conditions and Environment: Think about the conditions in which the equipment is to be used, such as temperature and humidity, and whether it will be exposed to corrosive substances. There are separators that are made for certain conditions and may be more effective and long lasting in those conditions.
For those looking to optimize their mineral processing, JXSC offers a wide range of high-quality magnetic separators. Click the best magnetic separator to explore our selection and find the perfect solution for your needs.
Customization and Optimization of Magnetic Separators
Magnetic separators can be customized and optimized to meet the needs of a certain application to ensure that it provides the best separation possible. Industries can improve separation efficiency, cut down the operating expenses and get better product purity by customizing the design and configuration. This includes choosing the right magnetic field intensity, controlling the geometry of the separator, and the right flow rate and particle size distribution.
JXSC provides modular design magnetic separators that can be tailored to meet the unique needs of your operation. Click customized magnetic separators to learn more about customizable solutions and achieve excellent separation in your processes.
Energy Consumption and Efficiency in Magnetic Separation
Energy is another important consideration in the use of magnetic separators since it determines the amount of energy required to power the magnetic separators. High efficiency separators not only lower energy consumption but also have a lesser effect on the environment. Newer magnetic systems have been developed to be energy efficient while at the same time providing high levels of separation. Such innovations include the use of permanent magnets which do not require constant supply of electrical power, and the improvement of the design of separators to increase the strength of the magnetic field and the efficiency of particle collection.
Optimised magnetic separation processes are energy efficient and help in minimising the emission of green house gases. It is evident that industries can save a lot of costs and contribute to the conservation of the environment by using magnetic separators that are energy efficient. Further studies and innovations in this area are still being carried out to enhance the efficiency of technology, making magnetic separation a sustainable and efficient separation process for use in different industries.
Conclusion
Magnetic separation technology has a bright future as researchers continue to work on improving its effectiveness, energy consumption and precision of the separation. High gradient and high intensity magnetic separators are some of the innovations that are believed to help in attaining better separation of fine and ultrafine particles. Furthermore, the application of smart technologies and automation will facilitate the continuous monitoring and enhancement of the separation processes, thus improving efficiency and lowering costs.
JXSC is in the leading position of these developments, and constantly improving technology, and with the help of a professional team to grasp the latest trends in the industry. Through research and development, JXSC guarantees that their customers are offered the best in magnetic separation technology, thus keeping them relevant in the market. The cutting-edge advancements and exceptional quality in magnetic separation technology by JXSC.
Want to discover cutting-edge advancements and exceptional quality in magnetic separation technology? Click https://www.minejxsc.com/ to explore more.
FAQs
How to maintain and clean magnetic separation equipment?
It is important to keep and clean the magnetic separation equipment to ensure that they work efficiently and last long. It is recommended that the equipment should be inspected from time to time to determine whether any of the parts are worn out and should be replaced. Cleaning is the process of washing the accumulated magnetic particles from the surface of the separator and this can be done by brushing or air blowing. In wet separators, the use of water or a cleaning solution can be used to flush out trapped particles.
How does magnetic separation contribute to resource recovery and recycling?
Magnetic separation is a critical process in the recovery of valuable materials and recycling of waste since it effectively separates ferromagnetic materials from waste. It also helps to improve the quality of the recyclable material and, at the same time, minimize the amount of waste that is dumped into the landfill. This is because by recycling the valuable metals, industries can be able to reduce their raw material costs and hence be environmentally friendly.
What are the environmental benefits of using magnetic separation?
Magnetic separation is environmentally friendly in waste management since it separates magnetic materials from non-magnetic ones to avoid polluting recyclable materials. The basic types of magnetic separators are energy saving and can treat a large amount of slurry within a short time, thus dealing with large volumes of process waste residuals. This method is especially used in mining and milling industries. Further, it is efficient in the removal of phosphates, hence reducing pollution of the environment. The externally applied magnetic field guarantees better separation, which in turn increases the yield of the desired material and reduces the amount of waste produced.
How does particle size affect the efficiency of magnetic separation?
Magnetic separation efficiency is highly dependent on the size of the particles. Particles that are smaller are harder to be separated and may need higher magnetic field or special separators. Uniformity of particle size distribution can improve separation efficiency because all the particles are exposed to the magnetic field in equal measure. Conditioning and sizing of the feed material can also improve the separation results and increase the purity of the product.