- Home
- Blog
- Equipment Info
- What is a Cone Crusher & How Does a Cone Crusher Work?
Introduction
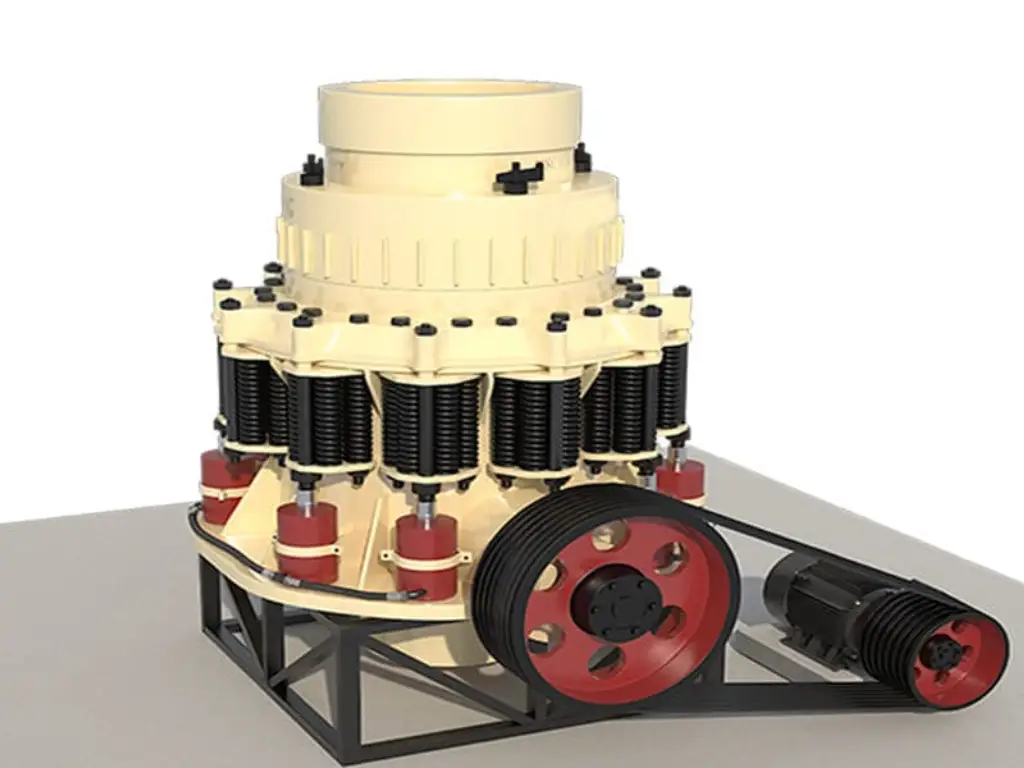
What is a Cone Crusher?
Cone Crusher Working Principle
The crushing cone’s axis experiences a powerful swing when the eccentric sleeve rotates. Importantly, this swinging movement causes the crushing wall’s surface to move in a way that continually approaches and recedes from the rolling mortar wall’s surface. The cone crusher operates on the basis of this dynamic action.
The actual stone crushing takes place in this ongoing operation between the mortar wall and the crushing wall. Inside the ring-shaped crushing chamber formed by the stationary cone and the moving cone, the material fed into the cone crusher undergoes an endless series of hits, squeezes, and bends.
Not only must force be applied, but it must be applied repeatedly, efficiently, and in a way that crushes the material from all sides. This is achieved by a combination of the cones’ clever placement and eccentric rotation. The material breaks down into smaller pieces until it achieves the desired size as it goes through this rigorous process of squeezing, striking, and bending. When sufficiently crushed, the material is discharged through the cone crusher’s bottom, prepared for the following stage of processing.
This methodical procedure demonstrates how the cone crusher can accurately and efficiently reduce large rocks into smaller, more manageable pieces. In order to satisfy the demands of contemporary mining, building, and aggregate usage, it functions somewhat like a combination of mechanical strength, material science, and technical acumen.
How Does a Cone Crusher Work?
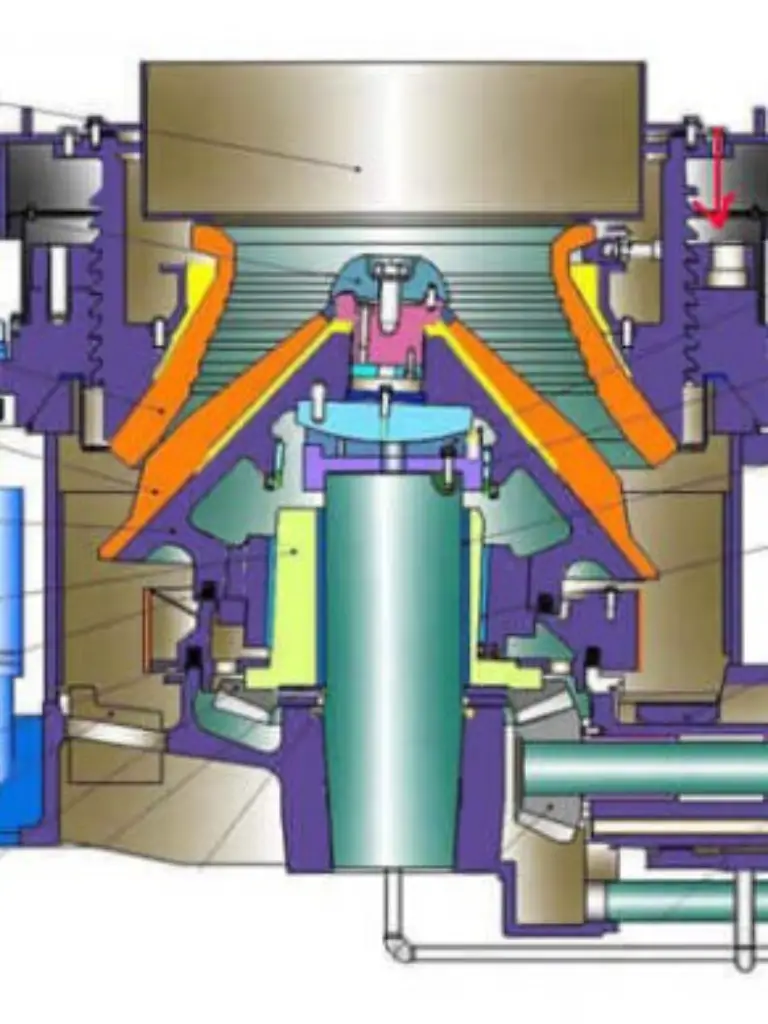
● Feeding the Crusher: The cone crusher’s feed hopper is filled with raw materials, such as rocks, ores, or recycled concrete, to begin the process. Automated systems or manual labor can be used to accomplish this. The material is subsequently directed by the hopper into the crushing chamber, which houses all of the action.
● Crushing Chamber Dynamics: Within the concave bowl of the crushing chamber, the materials come into contact with a rotating, conical mantle. The rock material is compressed and crushed between these two elements as the mantle travels closer to and farther away from the bowl. The material is crushed from all sides thanks to this circular motion, which increases the effectiveness of the size reduction process.
● Size Reduction: How small the material gets is all down to the closed side setting (CSS)—the tightest gap between the mantle and bowl while crushing. You can adjust this setting to change the size of the final output to match what you need.
● Applying Pressure: As the mantle spins, it doesn’t just move the rocks around. It also pushes them hard against the side of the bowl, which helps to crush them. The smaller the gap, the better the crushing works.
● Discharge from the Crusher: Once the rocks are crushed to the right size, they fall out of the bottom of the crusher through the discharge opening. The CSS setting decides how big or small the crushed rocks are at this point. A bigger CSS means bigger crushed rocks, and a smaller CSS means smaller crushed rocks.
● Continuous Operation: Raw materials are fed into the top of the crusher, and crushed materials are released from the bottom, making this a continuous process. Because of the crusher’s ability to handle huge amounts of material quickly, required crushed products can be produced continuously.
● Control and Adjustment: The people running the crusher can change the size of the crushed rocks by adjusting the CSS. Many modern cone crushers have special systems that let them quickly and easily adjust the CSS, which makes the crushing process more flexible and efficient.
Types of Cone Crusher
Feature | Spring Cone Crushers | Symons Cone Crushers | Compound Cone Crushers | Single Cylinder Hydraulic Cone Crushers | Multi-Cylinder Hydraulic Cone Crushers |
---|---|---|---|---|---|
Working Principle | Mechanical spring system for overload protection. | Advanced design with hydraulic tramp release and clearing systems. | Hybrid spring and hydraulic features, allowing quick adjustments and overload protection. | Single hydraulic cylinder used for adjusting the setting and clearing the chamber. | Several hydraulic cylinders for precise adjustment and efficient clearing. |
Adjustment & Safety | Manual adjustment, mechanical safety allows passage of hard materials. | Hydraulic adjustment, improved safety with hydraulic tramp release. | Hydraulic systems for adjustments, combines simplicity and safety. | Automated adjustments with a single hydraulic cylinder, enhanced safety. | Advanced automated adjustments, multiple cylinders ensure high safety levels. |
Capacity | Medium to Low | Medium to High | Medium | High | Very High |
Input/Output Size | Medium variability, less precise control. | Better control over output size, suitable for various stages. | Good control, suitable for a broad range of materials. | Precise control, ideal for medium to hard materials. | Precise control, excellent for producing fine sizes at high capacities. |
Operational Efficiency | Lower compared to hydraulic models, due to manual adjustments. | Higher efficiency, thanks to hydraulic adjustments and better clearing. | Balanced efficiency, benefits from both hydraulic and mechanical features. | High efficiency, simplified hydraulic operations reduce downtime. | Highest efficiency, multiple cylinders provide greater crushing force and speed. |
Application Suitability | Suited for medium-hard to hard materials, less automation. | Versatile, suitable for secondary, tertiary, and quaternary crushing. | Versatile, good for hard, abrasive materials. | Ideal for applications requiring medium to high productivity, with medium hardness materials. | Best for high-volume crushing of hard materials with need for precise size control. |
Key Components of Cone Crushers
Top Shell & Spider Cap Assembly
Main Shaft
Step Bearing
Mantle & Concaves
Eccentric Drive & Bushing
Pinion Gear & Countershaft Assembly
Bottom Shell
Adjusting the Cone Crusher for Optimal Performance

Closed Side Setting (CSS)
Reducing the CSS from, say, 25mm to 20mm, could refine the product size from a range of 30-40mm to 25-30mm, enhancing the product’s quality for specific applications. A smaller CSS generally results in a finer output, making it crucial for producing high-quality aggregate suited for more stringent specifications.
Open Side Setting (OSS)
Adjusting the OSS influences the crusher’s feed capacity. For instance, increasing the OSS from 50mm to 60mm might elevate the feed capacity from 200 tons per hour to 250 tons per hour, allowing the crusher to process more material within the same amount of time.
Eccentric Throw
Increasing the eccentric throw can enhance the crusher’s ability to crush and reduce material but might also produce a coarser product. For example, adjusting the eccentric throw from 20mm to 25mm could increase the particle size range of the product from 20-25mm to 25-30mm, impacting both the throughput and the size distribution of the product.
How to Operate Cone Crushers Professionally?
Common Industries and Applications of Cone Crushers
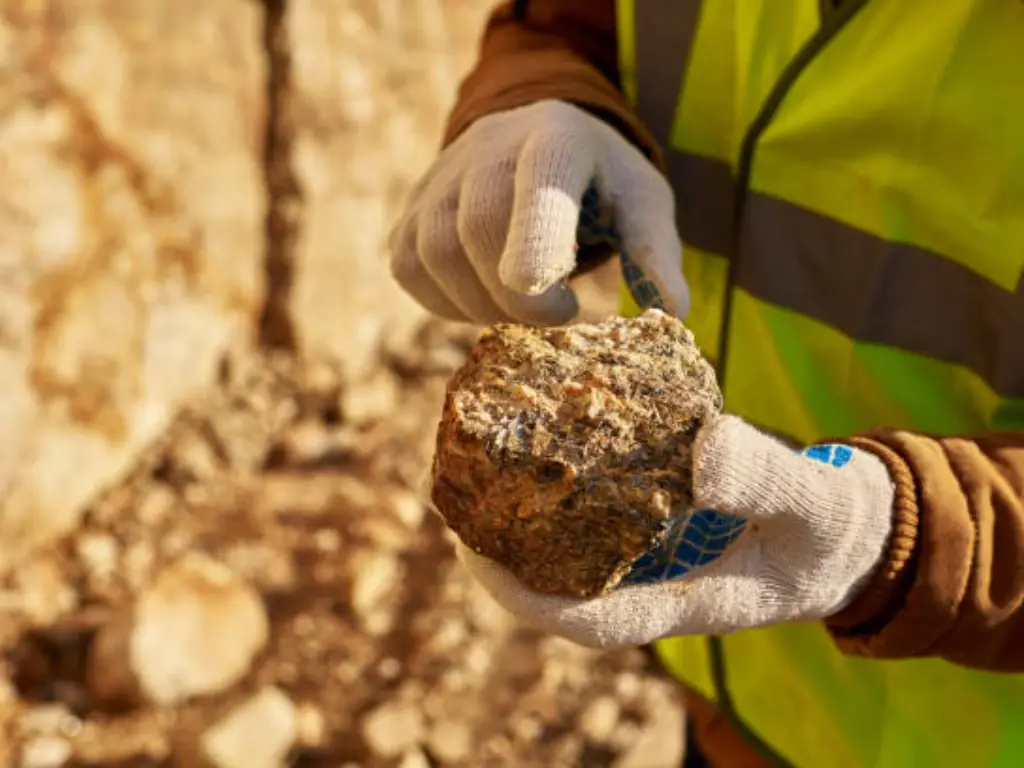
Applications
Advantages of Cone Crushers in Material Processing
Challenges and Limitations of Cone Crushers
While cone crushers work great in many different uses, they do face some specific challenges and limitations that can impact how efficient and productive they are overall.
● Material Compatibility: Cone crushers work incredibly well with ores, granite, and basalt. When things are going well, they break them down very nicely and don’t wear out too much. However, they have trouble handling goopy, squishy, or sticky materials like clay. These have the potential to clog the equipment and render it unusable.
● Product Uniformity: Cone crushers are quite versatile and can break down a wide range of materials, however achieving uniformly sized particles can be difficult. This is particularly valid for non-equally breaking materials. For other applications, such as the production of concrete or asphalt, where uniform particle size and shape are crucial, this restriction might not be the best option.
● Size Limitations: A cone crusher’s design places a limit on the largest raw material sizes that it can process. Overly large materials can clog pipes or necessitate multiple crushing steps in advance. This increases the cost and processing time overall.
● Operational Difficulties: Cone crushers are subject to high wear and tear, especially when processing coarse materials. This wear might result in downtime, which lowers overall production, in addition to raising maintenance expenses.
FAQs
What materials can be processed with a cone crusher?
What is the typical capacity range of cone crushers?
What are the key maintenance tips for a cone crusher?
Choosing the Right Cone Crushers for Your Mine Operations
JXSC Mineral Processing Equipments Bring You Convenience
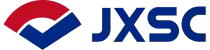