- Home
- Blog
- Equipment Info
- Types of Crushers 101 Guide: What You Should Know
- mmldigi
What Are Rock Crushers and How Do They Work?
Crushers are key equipment in mining, construction and aggregate industries. They break large rocks, ore, or other materials into smaller, more usable pieces. This equipment reduces the material by means of compressive force, impact, attrition or shear that are specific for the type of crusher being used. The main function of an industrial rock crusher is to generate particles of similar sizes. These particles can be further purified for use in other applications, including road construction, building materials, and raw materials for other industries.
The crushing process is commonly conducted in several stages. Each stage of the crushing process implements a different type of crusher to gradually reduce the size of the material. The first step is crushing the material by using larger crushers that can reduce the material into smaller sizes that will be used in the next stage. Following this, the secondary and tertiary stages are employed to further reduce the particle size using smaller crushers until the desired output is achieved. During the process, screens are utilized in order to segregate the crushed material into various size fractions. This guarantees that the end result has the needed specifications.
Crushing Methods: Compression, Impact, Attrition, and Shear
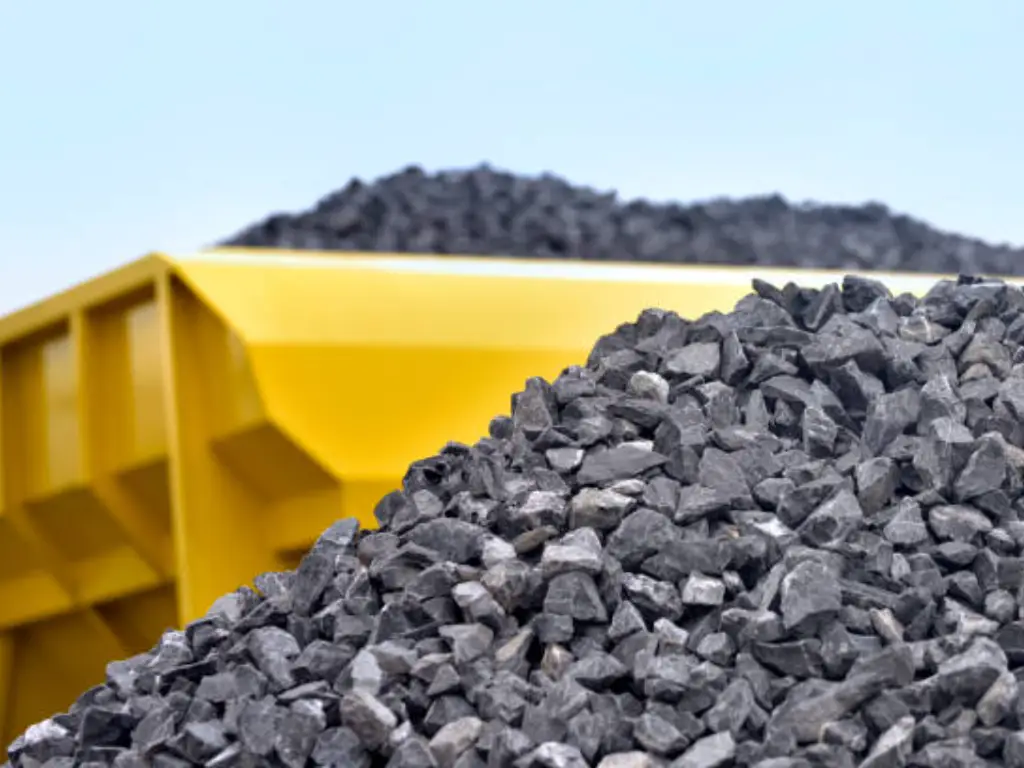
● Impact Crushing: The process called impact crushing involves the repeated striking of the material with a very fast rotating element, for instance, a rotor with the attached hammers or blow bars. Impact crushers and hammer mills work with it. In impact crushers, the material is hit by rotating hammers or blow bars, as a result it breaks up into smaller pieces. This method is preferable in the case of less abrasive materials, such as limestone, dolomite, and soft to medium hard rocks. The high-speed impact forces can wear down the crushing elements rapidly when processing very abrasive materials.
● Attrition Crushing: Abrasion crushing is the consequence of material being subjected to the grinding action, often between two rotating surfaces or media. This is the reason why there is a decrease in particle size due to abrasion and friction. This method is popularly employed in fine grinding processes such as ball mills or rod mills. In these mills, the material is blended with grinding media, for instance, balls or rods made of steel. The rotation of the mill makes the media grind and wear out the material, thus lowering its size in stages. Atrition crushing is great for the production of very fine particle sizes and it is commonly used in mineral processing and mining for grinding ore.
● Shear Crushing: Shear crushing takes a shearing force and applies it to the material, which results in the formation of cracks on the weak planes. This method is not frequently used in rock crushing applications but can be found in some specialized equipment, like roll crushers, for example, for softer materials like coal or clay. In roll crushers, the material is pulled between two counter-rotating rolls which exert a shear force on it. The material breaks and reduces in size due to this force. This kind of crushing works better for materials that have a layered or flat structure because the shear forces can easily split the material along the weak planes.
What are the Different Types of Crushers?
Type of Rock Crusher | Description | Application | Feed Size | Output Size | Capacity | Advantages | Limitations |
---|---|---|---|---|---|---|---|
Jaw Crusher | Uses a reciprocating jaw to compress and crush material against a stationary plate | Primary crushing stage, handles large, abrasive materials | Up to 1,500 mm | 50-300 mm | Moderate to high | Simple design, reliable, handles abrasive materials | Limited reduction ratio, lower capacity compared to gyratory crushers |
Cone Crusher | Uses a rotating mantle within a concave bowl to compress and crush material | Secondary and tertiary crushing stages, offers better shape and size control | 50-300 mm | 6-100 mm | Moderate to high | Better shape and size control, higher reduction ratio | Higher capital and operating costs, more complex design |
Impact Crusher | Uses high-speed rotors with attached hammers or blow bars to strike and break material | Suitable for less abrasive materials, produces a more cubical product shape | 50-500 mm | 5-100 mm | Moderate to high | Produces cubical shape, handles softer materials well | Higher wear on crushing elements, not suitable for highly abrasive materials |
Gyratory Crusher | Uses a rotating mantle within a concave surface to compress and crush material | Large-scale primary crushing applications, high capacity | Up to 1,500 mm | 100-300 mm | High | High capacity, continuous operation, higher reduction ratio | Higher capital and operating costs, more complex design and maintenance |
Hammer Mill | Consists of a series of hammers mounted on a rotating shaft that strike and break material against a screen or plate | Suitable for softer materials, produces finer particle sizes | 50-500 mm | 0.1-20 mm | Low to moderate | Produces finer particle sizes, handles softer materials well | Higher wear on hammers, not suitable for highly abrasive materials |
Roll Crusher | Uses two or more rotating cylinders to compress and break material | Typically used for softer materials, such as coal or clay, produces a finer product | 50-500 mm | 2-50 mm | Low to moderate | Lower energy consumption, handles softer materials well | Limited reduction ratio, not suitable for highly abrasive materials |
Primary Crushers
Jaw crushers and gyratory crushers are the two most common kinds of primary crushers. These crushers apply compressive forces to the material, but they can be different in their design and the way they operate.
Jaw Crushers
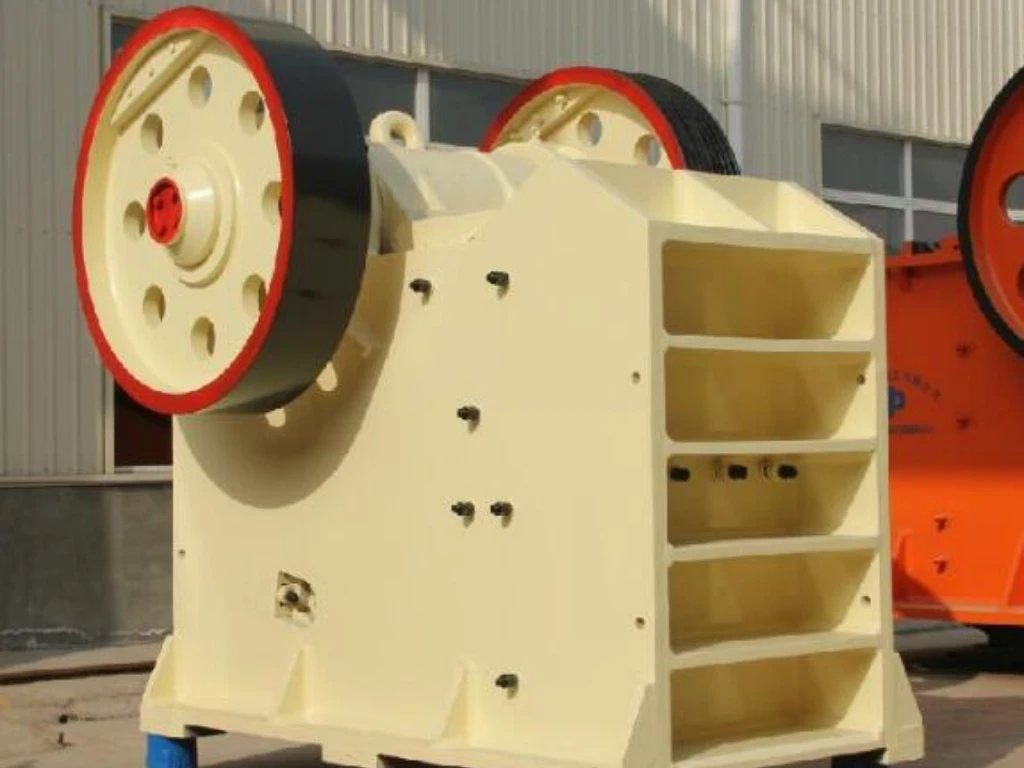
Jaw crushers are the most common primary crushers used in the mining and construction industry. They are represented by a fixed jaw and a moving jaw that form a V-shaped crushing chamber. The moving jaw moves back and forth and presses the material against the fixed jaw, that in turn causes it to break down into smaller pieces. Jaw crushers are known for their simplicity, reliability, and the ability to manage large and abrasive materials. They take in feed sizes as large as 1,500 mm and the finished product size ranges from 50 mm to 300 mm depending on the settings of the crusher and the material properties.
There are two main types of jaw crushers: simple-toggle and double-toggle. A single-toggle jaw crusher is simpler in design and is widely used because of its low cost and ease of maintenance. On the one hand, the double-toggle jaw crushers have a more complicated mechanism that creates a more uniform product size and a more efficient crushing. On the other hand, they are often more expensive and require higher maintenance than single-toggle ones.
Jaw crushers are ideal for primary crushing and can handle large, hard materials like granite and basalt.
Gyratory Crushers
Gyratory crushers are also another primary crusher type which is usually used in large scale mining operations. They are equipped with a vertical conical crushing chamber with a rotating mantle that moves inside a stationary concave surface. The mantle is rotating and the material is getting compressed against the concave surface thereby it breaks and becomes smaller. Gyratory crushers are valued for their high capacity, continuous operation, and ability to process feeds up to 1500 mm in diameter.
Unlike jaw crushers, gyratory crushers generally have higher reduction ratios. Consequently, they can produce smaller output sizes in a single pass. Moreover, they have a higher production capacity and can do more material per hour. Nevertheless, gyratory crushers are usually more expensive, need more intricate foundation and have higher operating and maintenance costs as compared to jaw crushers. The decision of a jaw crusher or a gyratory crusher is based on, for instance, the required output size, production capacity, and the available budget.
Gyratory crushers, often compared to jaw crushers, excel in processing very hard materials like granite and ores.
Secondary Crushers
Secondary crushers can be divided into three main types: cone crushers, roller crushers, and impact crushers. All types of crushers have their own distinctive design, working principles, and applications.
Cone Crushers

Cone crushers are usually applied in the secondary and tertiary crushing. They also play a role in reducing the size of the material coming from the primary crusher. They include a rotating mantle which moves within a stationary concave bowl. It does this by squeezing and squeezing the material as it goes through the device. Cone crushers are often used because they are capable of producing a product with a more uniform and cubical shape as opposed to jaw crushers. This is what makes them suitable for the industry where particle shape is of utmost importance, such as in the production of concrete aggregates.
There are various cone crushers, such as standard cone crushers, short head cone crushers and fine cone crushers. A standard cone crusher has a taller crushing chamber and is used for providing larger output sizes, usually ranging between 25 mm and 100 mm. A short-head cone crusher has a short crushing chamber and it is designed for the production of finer output sizes, generally between 6 mm and 25 mm. A fine cone crusher, also known as a tertiary cone crusher, is used for the production of They are manufactured to produce very fine output sizes, mostly below 6 mm, particularly for medium-hard to hard materials such as limestone and dolomite.
To understand cone crushers in detail, check out What is a Cone Crusher & How Does a Cone Crusher Work?
Roller Crushers
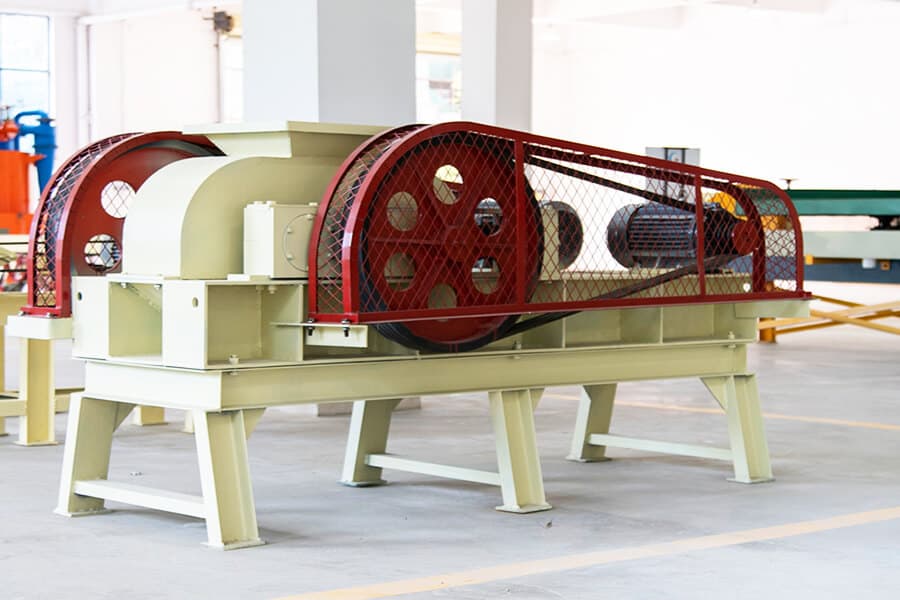
Roll crushers are another type of secondary stage crushers. They use two or more rotating cylinders for compressing and breaking down the material. The cylinders can be smooth or toothed, based on the different application and type of material. Roller crushers are usually applied for soft materials, for example, coal, clay or soft rocks. They can give a finer end product as compared to other types of crushers. They are also recognized for their low energy usage and fairly low wear on the crushing surfaces.
There are two main types of roller crushers: single-roll crushers and double-roll crushers. Single-roll crushers are equipped with a rotating cylinder which squeezes the material against a fixed plate or screen. The double-roll crushers, in contrast, are equipped with two rotating cylinders that compress the material between them. The double-roll crushers can be further divided into the smooth-roll crushers that have the smooth cylinder surfaces and toothed-roll crushers that have toothed or corrugated surfaces to provide the better grip and crushing action.
Roll crushers are best for reducing softer, friable materials like coal, salt, or limestone.
Impact Crushers
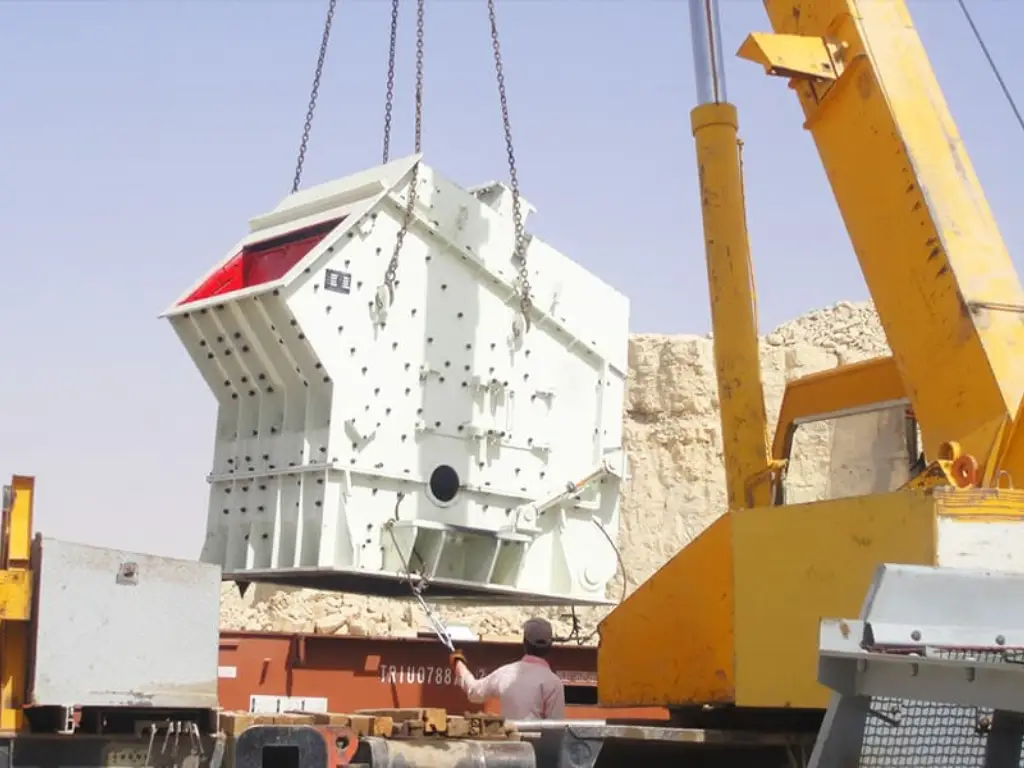
Impact crushers are the secondary crushers or the tertiary crushers that use high speed impact forces to break the materials. They are a set of rotors with hammers or blow bars mounted on them that crush the material as it enters the crushing chamber. This phenomenon results in the material to be cracked and fragmented into smaller pieces. The impact crushers are applicable for less abrasive materials such as limestone, dolomite, and soft to medium – hard rocks. They can generate a more cubical and uniform product shape which compression crushers do not have.
There are two main types of impact crushers: horizontal shaft impactors (HSI) and vertical shaft impactors (VSI). HSI crushers utilize a horizontal rotor that throws the material on stationary anvils or curtains, which results in the material breaking upon impact. VSI crushers, unlike the traditional crushers, have a vertical rotor which accelerates the material and throws it against a stationary anvil ring or a cloud of material itself. Hence, the shape of the product is more cubical and uniform. VSI crushers are commonly used in the last stage of the crushing process in order to enhance the particle shape and eliminate deformed or elongated particles.
Hammer Crusher: A Versatile Solution for Multiple Materials
Hammer crushers are widely used in the mining, cement, coal, metallurgy, construction, and other industries for primary and secondary crushing. They are equipped with a rotor with multiple hammers, which apply high speed impact to break down materials, and are a reliable and efficient solution for materials such as coal, gypsum, limestone and soft ores. The hammer crusher is designed to crush the materials into smaller pieces by the hammer of the hammer crusher.
Single stage and multi stage are the two main types of hammer crushers. Single stage hammer crushers are simpler in design and are widely used for applications where a coarse product size is acceptable. These crushers are cheap and require little maintenance. However, multi stage hammer crushers offer more control over the final product size and shape, which is important when a finer, more consistent output is required. But they are more complex and expensive.
Hammer crushers are used for breaking down softer materials such as coal, clay, limestone, etc. with high moisture content. They are efficient for large scale operations due to their high throughput capacity and low energy consumption. In particular, these machines are very useful when large quantities of material need to be processed quickly and efficiently.
Tertiary and Quaternary Crushers
● Fine Cone Crushers: These are cone crushers with a very short crushing chamber and a specific design. They are manufactured to produce fine output sizes in the range of 0.078 inch to 0.236 inch.
● Vertical Shaft Impactors (VSI): VSI crushers are employed in tertiary and quaternary stages. They contribute to particle shape and yield uniform, cubical products.
● High-Pressure Grinding Rolls (HPGR): In the HPGR crushers two counter-rotating rollers with a small gap between them are used. They squeeze and crush the stuff. They are very good at fine grinding and are often used in the mining industry for the grinding of ore.
● Autogenous and Semi-Autogenous Mills (AG/SAG): AG and SAG mills are large, rotary drums that use the material itself as the grinding medium. They can be used in the final stages of the crushing operation to produce fine uniform particles.
The selection of tertiary and quaternary crushers depends on various parameters. These are the specialized application, material properties, and the output size and shape which are required. In other cases, a mixture of different crushers types may be used to produce the best results.
Factors to Consider When Choosing the Right Crusher for Your Application
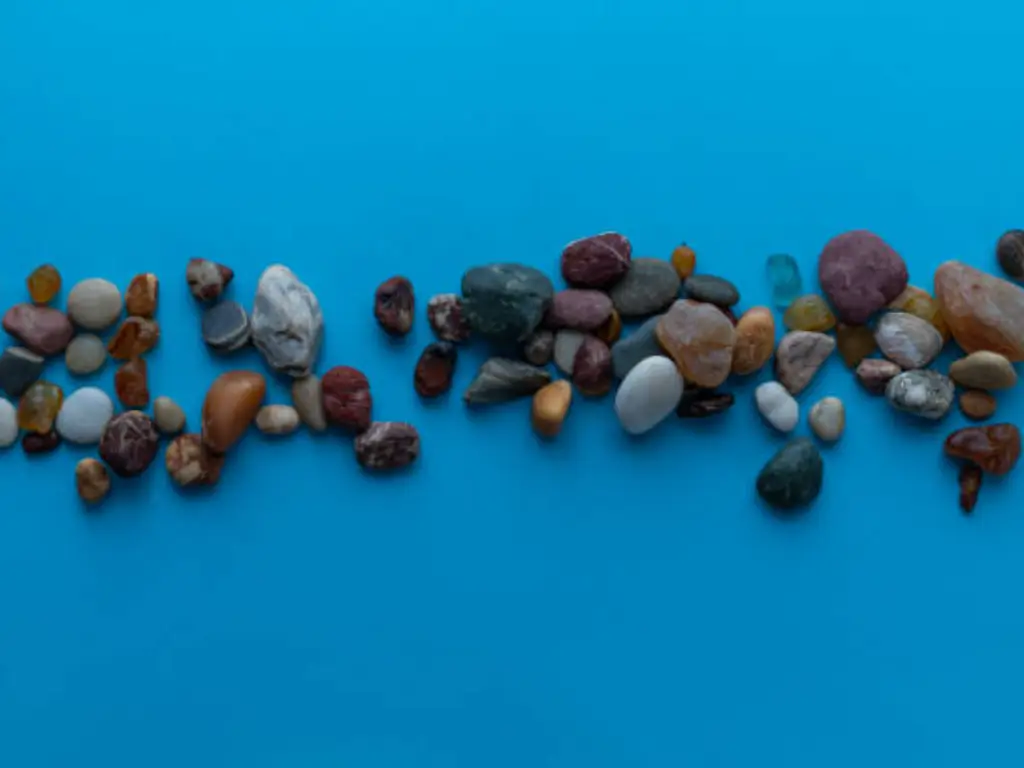
Material Properties:
Feed Size and Output Size:
Production Capacity:
Product Shape and Gradation:
Operational Considerations:
Capital and Operating Costs:
Footprint and Layout: