- Home
- Blog
- Equipment Info
- How Does a Rock Crusher Work? Choose the Right Machine
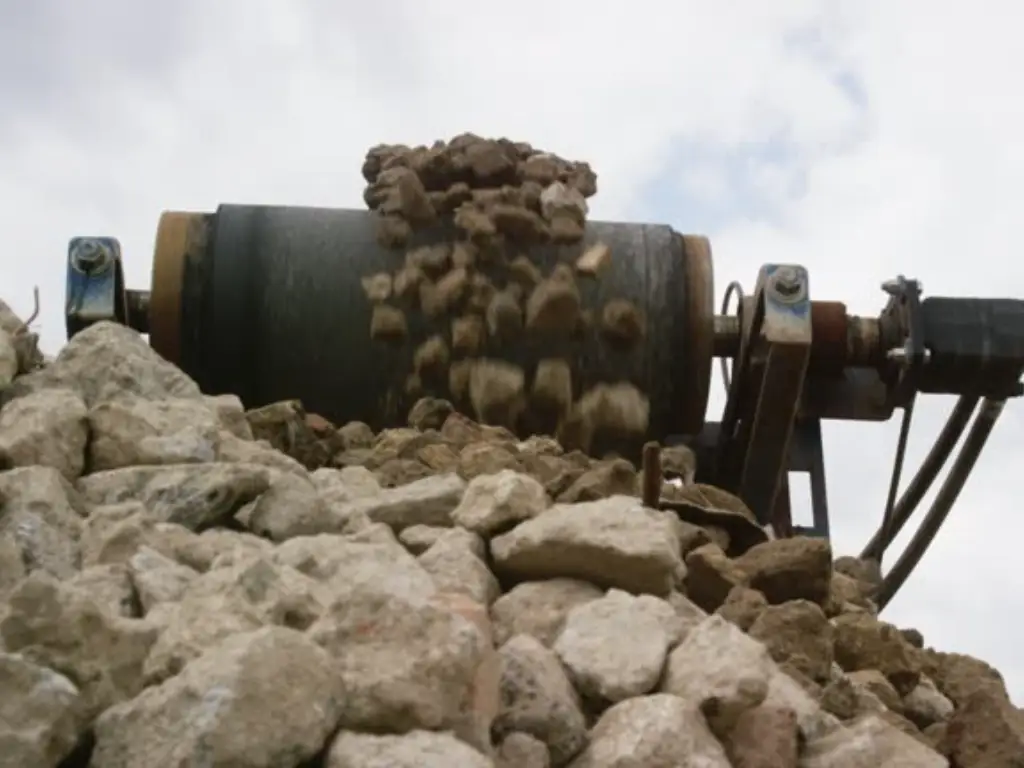
In the sectors of the mining industry, construction, and recycling, raw materials frequently originate from massive and weighty forms – rocks. Metamorphosing untamed geological mass is a fundamental, albeit initial, step required to transform these raw materials into usable aggregates, refined ores, or even waste requires further processing.
A powerful industrial revolution machine designed to break down large stones into smaller rocks is called a rock crusher, and it’s responsible for the initial stages of this process.
Reviewing and analyzing the rock crushing mechanics is the first step in decision-making process, unlike what people perceive as theoretical. It will allow you to choose appropriate equipment for a specific task and inspect efficiency, cost, and end product value dominantly impacted by such decisions. In this article, I will detail the workings of a rock crusher and empower you to make the principles-guided decision of selecting the appropriate machine.
Understanding Rock Crushers: What They Are and Why They Matter
Essentially, a stone crusher is an industrial piece of equipment that mechanically reduces the size of large rocks and other materials. When stone, ore, or cement is crushed, it is turned into a fine material consisting of tiny pieces, which can be sand, gravel, or other tailored sizes needed for industrial or construction work.
From preparing the ore in mining to reclaiming concrete and asphalt in recycling, stone crushers are significantly useful in various fields. In construction, stone crushers break down large pieces of stone to create building aggregates for concrete.
Fragmented materials are cheaper to transport; therefore, efficient size reduction increases profits and optimizes the downstream processes. They also offer an array of initial feed materials to deal with and unique output characteristics, where most deal with coarse material.
Here’s a summary of some common types and what they typically process:
Crusher Type | Primary Crushing Method | Typical Feed Material Size (Approx.) | Material Hardness Range (Mohs Scale Appx.) | Common Materials Processed | Suitable Stages |
---|---|---|---|---|---|
Jaw Crusher | Compression | Up to 1500 mm (Primary Feed) | 5 - 8 (Very Hard to Hard & Abrasive) | Granite, Basalt, Hard Ore, Concrete, Asphalt | Primary |
Gyratory Crusher | Compression | Up to >1500 mm (Large Primary Feed) | 5 - 8 (Very Hard to Hard & Abrasive) | High-Capacity Mining Ore, Hard Rock | Primary |
Cone Crusher | Compression | 50 mm - 400 mm (Output from Primary) | 5 - 8 (Hard to Medium Hard & Abrasive) | Granite, Basalt, Ore, Gravel | Secondary, Tertiary |
Impact Crusher (HSI) | Impact | Up to 500 mm (Secondary/Tertiary Feed) | 3 - 5 (Medium Hard to Soft, Less Abrasive) | Limestone, Concrete, Asphalt, Soft Rock | Secondary, Tertiary |
Impact Crusher (VSI) | Impact / Attrition | 0 mm - 80 mm (Output from Secondary/Tertiary) | 5 - 8 (Hard to Medium Hard & Abrasive) | Manufactured Sand, Fine Aggregate, Shaping Abrasive Rock | Tertiary, Quaternary |
Roll Crusher | Compression / Shear | 0 mm - 150 mm | 2 - 4 (Soft to Medium Hard, Friable) | Coal, Phosphate, Clay, Friable Ores | Secondary, Tertiary |
How Rocks Get Broken: The Basic Methods
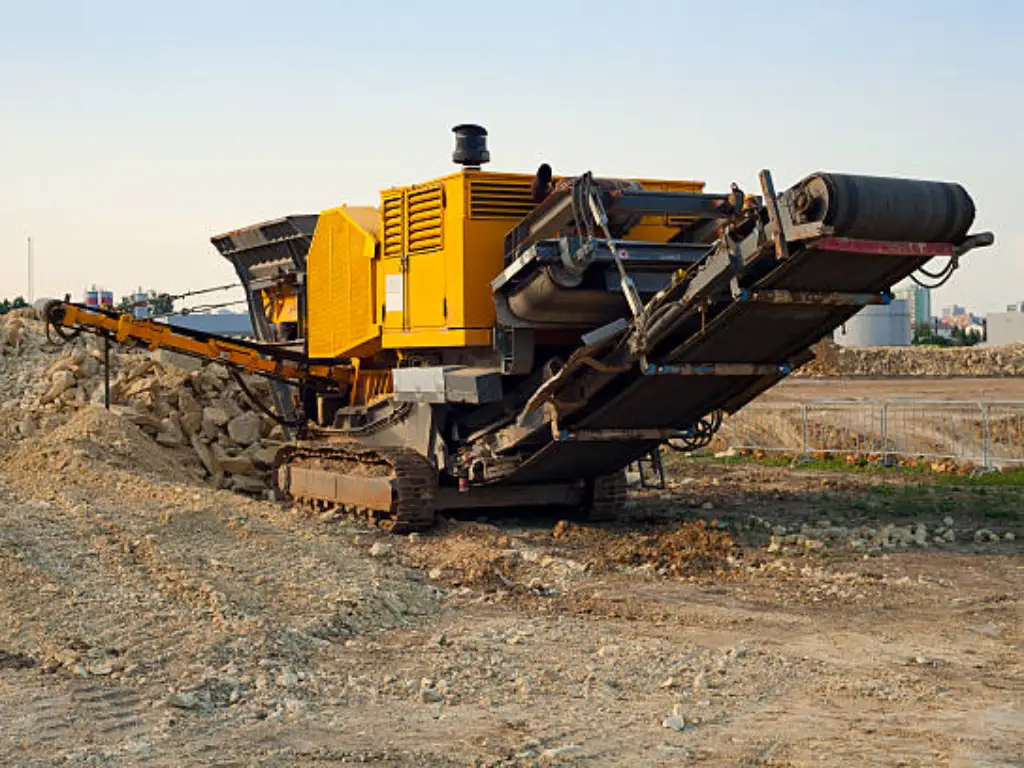
Given ample force, mechanical rock crushers are able to break rocks. The process must take into consideration different mechanical principles that achieve this set goal:
● Compression: Rocks can be squeezed between solid surfaces. By reducing the space between two parallel plates containing the rocks, the rock particles undergo an increase in pressure until their internal bonds break and fracture the material. Think of it like putting a nut in a nutcracker – the shell (rock) breaks under squeezing force. This compressive force causes the rock’s molecules to separate or change alignment.
● Impact: With this method, rocks are broken by delivering one heavy blow or series of blows at high speeds to achieve favorable results. During this part of the procedure, the rock is shattered like glass along existing weak points and fractures. One can visualize smashing a small stone with a hammer. The stone will break apart on impact. During ancient times, trip hammers used were an extremely innovative method that set the standard of applying impact.
● Shear / Attrition: This occurs when forces are applied in parallel to the surface, leading to layer materials sliding and subsequently breaking apart, or when rocks to rub against one another or against some surfaces within the wear parts of the crusher. This method works particularly well for producing finer materials and improving the shape of the particles.
● Grinding: More typical of grinding mills, which are employed as auxiliary equipment after crushing, grinding is described as reduction in size caused by rubbing action and abrasion which converts the material into rock dust or very fine powder. Some crushers make use of attrition which is a form of grinding action on the coarse particles.
There are various classifications of crushers based on how they work to transform energy which mostly focus on one or more of the principles above to reduce size.
Compressing Rocks: Jaw and Cone Action
Compression is perhaps the most intuitive method of rock crushing, and it is the primary force employed by two of the most common crusher types: the jaw crusher and the cone crusher.
Jaw Crusher:
Jaw crushers incorporate a stationary and a movable jaw (swing jaw) to create a V-shaped crushing chamber. This fixed feed region accommodates the large incoming rock. The oscillating, moving-up, or shrugging jaw, working via a toggle plate and eccentric shaft system, compresses rock that is added into the top of the chamber. Often lined with wear-resistant manganese steel parts, jaws do, however, wear out. The jaw crushers rely upon the reciprocating movement of the movable jaw. During every jaw cycle, the rocks are compacted until they become smaller fragments that can drop down to be further compressed in another tapered chamber by the swing jaw’s motion. The swing jaw compression movement will repeat until the material is sufficiently pulverized to be discharged through the controlled variable outlet gap at the bottom of the jaws, set by the closed side setting (CSS). One of Blake’s jaw crushers, designed and patented by Eli Whitney Blake, displays this principle with its upper pivot point yielding apex centric ‘dive’ action crushing, as opposed to Dodge’s bottom pivot centrifugal ‘rise’ action.
Cone Crusher:
Typically used in the secondary and tertiary stages of crushing, cone crushers also perform tasks using compression, although in a more refined and continuous fashion. A cone mantle (the moving crushing part) and a concave surface bowl liner (the part which remains stationary) comprise its parts. The stationary part surrounding the cone also called a bowl, holds a central shaft. An eccentric shaft powers the mantle which simultaneously turns the shaft, causing it to have a constant changing gap with the bowl as the gap shifts and moves with the shaft rotation. Initially, material is fed through the top opening of the frame body and is pulled into the space between the bowl and mantle where it is crushed. Material is allowed to fall lower when the mantle moves away but this stage cannot empty the chamber. Through cyclic compression and flow, materials are pushed upward through the bottom opening until finely ground enough to be useful. The cone is somewhat like a mechanized mortar and pestle, continuously grinding and effectively achieving a smaller output than traditionally obtained with jaw crushers.
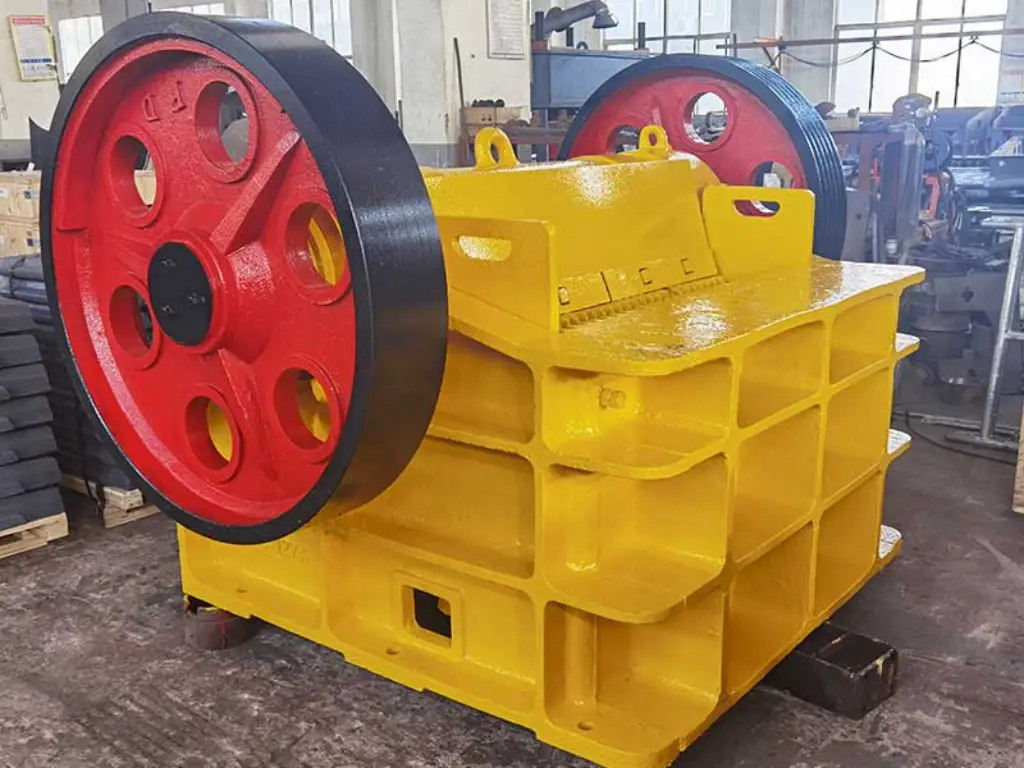
Smashing Rocks: How Impact Crushers Break
The impact crushers are a completely different method in size classification because they use high-speed impact as opposed to steady compression. Less abrasive material like limestone or aggregates that need to be cubical are best processed with impact compression. Horizontal Shaft Impactors (HSI) and Vertical Shaft Impactors (VSI) are the two primary types.
HSI:
In Horizontal Shaft Impactors (HSI), a rotor with blow bars or hammers is fastened to its edge. The rotor is spun rapidly, and starting material placed in the crushing chamber is struck with a heavy, rotary action by these bars, which sends the material hurtling toward the impact plates or aprons situated around the walls of the chamber. The rock will break up on the plates and also as the further associated reduction takes place when the crushed material re-encounters the rotor or other particles. This is like very powerful fists attacking the incoming rock. The spacing between the blow bars and the impact plates, which determine the output size, are frequently adjustable.
VSI:
While Vertical Shaft Impactors (VSI) do utilize impact, they operate on a different principle. The material feed is put into the center of a high-speed rotor that accelerates it outward towards wear-resistant shoes or tips. The make-up is unusually ejected from the rotor at scorching speed. Either stationary a rock bed is impacted (stone-on-stone crushing meaning effectively crushing new rock against previously crushed material) or wear-resistant anvils (stone-on-steel crushing) within the surrounding crushing chamber. Due to the immense velocity of the impact, the rock is bound to break, especially along natural stress points. VSI’s rotate with centrifugal action that is somewhat like a centrifuge that flings material outward. This method is excellent for producing cubical products and is often executed in the tertiary or quaternary stages, or for sand manufacturing.
Beyond Impact: Other Ways Machines Crush Stone
Even though compression and impact are the primary principles, other variations or combinations n other types of crushers are employed to suit specific materials.
Gyratory crushers operate on the same principle as cone crushers, with the significant difference that they are much larger and mainly used for primary crushing in large-scale operations, frequently found directly beneath the mining shovels. They are equipped with a massive conical head which gyrates around the main shaft within a fixed concave surface liner. Their robust construction permits use with coarse materials from open-pit mines, like the primary shovels, they process enormous feed sizes.
Roll crushers, whether single, double, or triple roll design, achieve these objectives primarily by using compression and shear forces. The starting material is drawn into the space between one or more pairs of counter-rotating cylindrical rollers and is crushed as the rotating rollers apply increasing pressure. They are useful for crushing materials such as coal, soft ores, and some minerals that are brittle in nature and where the generation of fines is undesirable or has to be controlled.
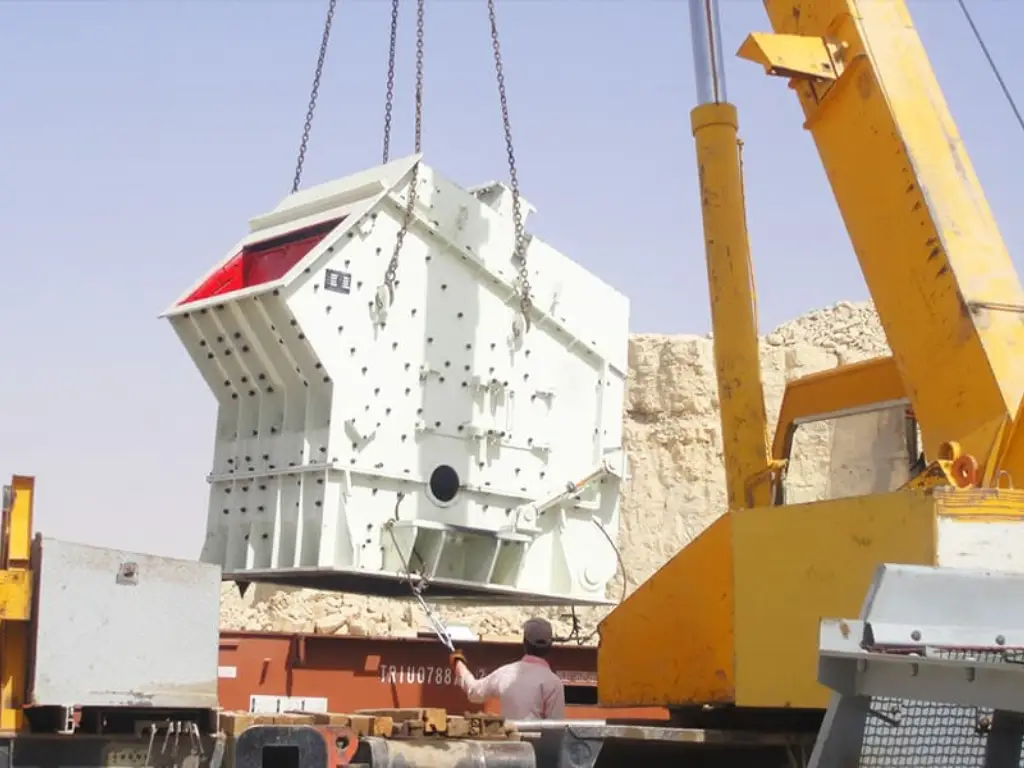
The Step-by-Step Crushing Process
An individual machine does not achieve size reduction in large scale operations. Instead, size reduction takes place in a series of crushing stages. With this multi-stage procedure, efficiency optimization, enhanced control over the diverse range of output sizes, as well as protection for downstream equipment is ensured.
● Primary Crushing: During this first stage, primary crushing is responsible for handling Run Of Mine (ROM) material that is excavated or blasted. The aim during this stage is to reduce extremely large rocks, which is frequently the maximum size of raw material, to a size manageable by secondary crushers. Coarse material is efficiently handled by primary crushing machines like jaw and rotary crushers.
● Secondary Crushing: Output coming from the primary crusher is processed during this stage. Secondary crushing also uses tighter and higher throughout crushers since the material has already been reduced in size. These graders start off with defining preliminary order of the output’s gradation by further reducing the size. Horizontal Shaft Impactors and Cone Crushers are commonly used in this stage.
● Tertiary Crushing: Tertiary crushing is the step that follows secondary stage if the requirement is for finely crushed material or specific particle shapes. Typical tertiary crushers are short head types of cone crushers and Vertical Shaft Impactors which utilize high levels of impact centrifuge rotation to simultaneously hurl material at high velocities.
Separating machines are present among each pre-crushing to sort out the material that has been crushed and has attained the preferred dimension to free the material from the subsequent crusher and processes, thereby improving efficiency, reducing wear, and streamlining operation transport.
Choosing Your Crusher: Why Expertise Helps
It’s important to grasp how different rock crushers function, the principles behind their operation, and how they fit into multi-stage workflows. But this understanding becomes challenging when it comes to selecting the appropriate crushing machine for a specific project.
Making the right choice involves careful evaluation of many aspects: the characteristics of different materials you plan to crush (hardness, abrasiveness, moisture content, feed size distribution), your expected throughput capacity, the site’s restrictions, operating expenses (especially maintenance costs like replacing wear parts such as manganese steel and energy consumption), budget, and the shape and size of the output particle. A precision impact crusher is bound to fail when attempting to crush abrasive granite, while limestone is impact-friendly limestone ultimately leading to its soft compression-friendly limestone. Primary crushers optimized for high tonnage throughput won’t be able to fine cube the aggregate required for asphalt production which needs VSI action and precision impact targeting shape and dimensions at high speeds. Other considerations should include the variable discharge area and its relevance to output control and transportation for downstream processes.
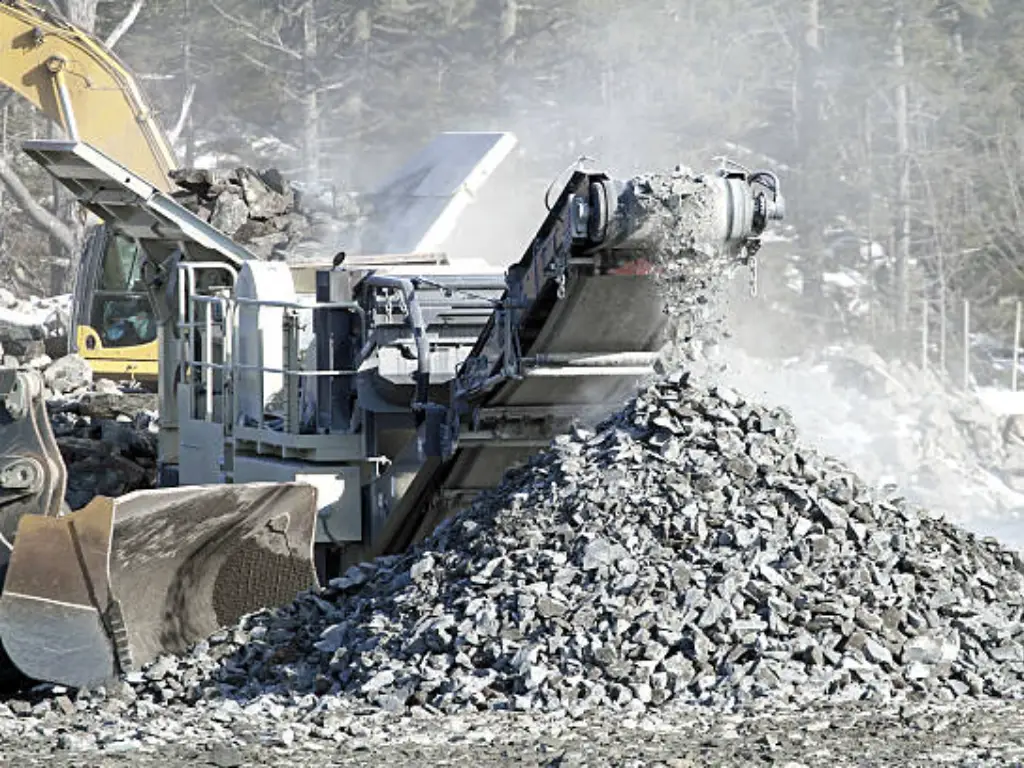
JXSC: Professional Rock Crusher manufacturer
This is where JXSC’s experience as a mineral processing equipment manufacturer provides value. We do not only offer machinery; we offer machinery with comprehensive jaw crushers, cone crushers, impact crushers, and all other types in this article, along with decades of global multi-material project experience and practical use understanding. We understand your production output target and have the knowledge the start material characteristics to recommend a custom crushing solution. That is the appropriate types of stone crushers, the best suitable order of crushing stages (if quaternary crushers are necessary), and the precise configurations for ideal efficiency and final granule size optimization, transport and process robustness, and cost-efficiency.
JXSC equipment www.minejxsc.com is known for its high quality and reliability. The crushing machines are professionally advised and supported after sales throughout the whole process, in such a way that all guarantees after the sale are fulfilled, which secures the value of the equipment relative to the price paid. Choosing critical equipment with a guess is bad business. It is better working with the professionals who know the science behind the break. If you rely on costly equipment, trusting them without first validating their protocol engineering recently as a shock to the system, kindly reach out to experts on the subject.
Conclusion
Crushing rocks into smaller, more manageable pieces, be it through compression, impact, shear, or even grinding, is a captivating application of mechanical advantage and mechanical force, as jaw, cone, and impact specialized stone crushers are capable of functioning as primary, secondary, tertiary, and even quaternary crushers.
Understanding each individual type of crusher is crucial.
Selecting the most suitable crushing machine is no easy task. The starting material, desired particle size, required capacity, site conditions, and even the method used for transporting the material later in the process all need to be taken into account.
This is where JXSC can help. With years of experience in crushing principles, manganese steel wear parts, dynamics of eccentric shafts, and variable discharge area controls, we ensure that every customer is provided with the best possible option tailored to their material handling project.