- Home
- Blog
- Mineral Solution
- How is Lithium Mined: Understanding the Methods and Techniques
- mmldigi
Introduction
Lithium, the main component in modern battery technology, has had a long history of energy storage since its discovery in the 19th century. Lithium mining has developed substantially to match the increasing needs of all the industries, especially renewable energy. The United States and South America are significant producers of lithium with the latter being the place where the largest lithium reserves are located in the world. Lithium salts, like lithium carbonate and lithium hydroxide, are the major products of lithium mining. The latest developments in direct lithium extraction technologies have the capability of changing the industry through the increase in efficiency and lessen the environmental impact. With the increasing demand of the world for lithium, it will be vital to implement sustainable and innovative lithium production methods that will support the global transition to renewable energy, including the world’s lithium reserves.
How Is Lithium Mined?
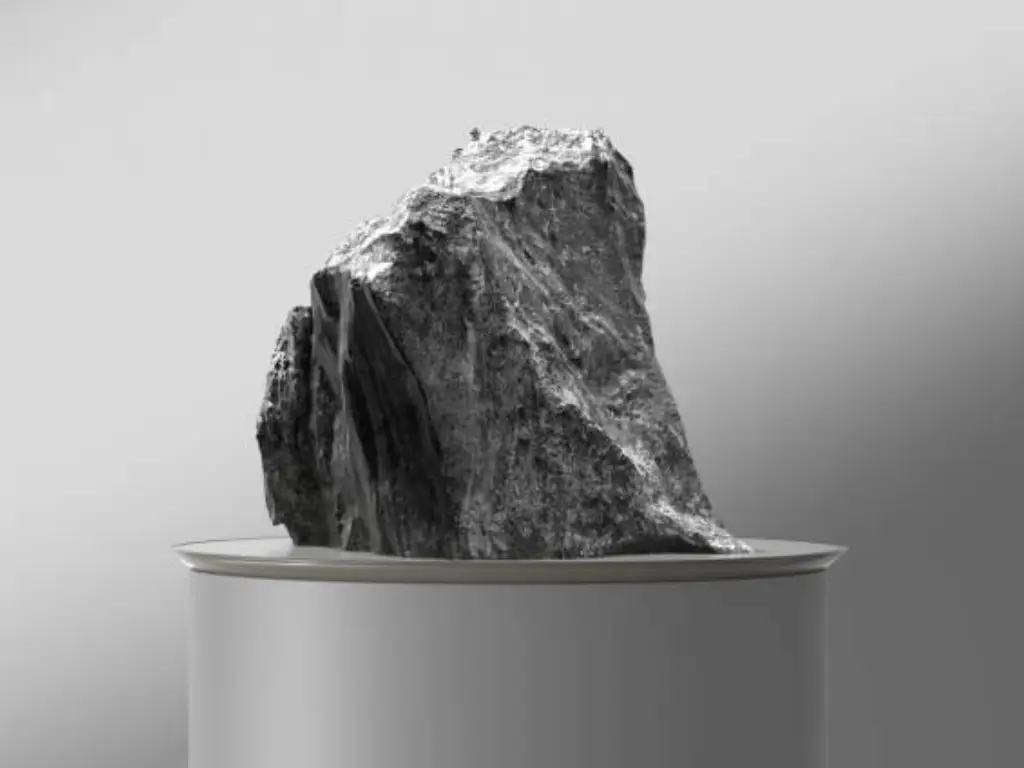
The General methods
Lithium is extracted through different methods, usually, salt-flat brine extraction and hard rock mining.
Salt-Flat Brines
Salt flats, most of which are in the “Lithium Triangle” of Chile, Argentina, and Bolivia, play an important role in lithium production. The lithium extraction process entails pumping the brine into the evaporation ponds. There, the water evaporates and the lithium concentration increases. The brine is then purified to generate lithium chloride or lithium carbonate. Traditional brine extraction, nevertheless, has drawbacks which include high water consumption and possible environmental consequences. To deal with these problems technologists are developing new technologies to get lithium from salt flats and as a result they try to decrease the water consumption, increase the efficiency and minimize the environmental impact. With the lithium demand expected to rise, sustainable lithium extraction from salt flats will be equally important to the shift to sustainable energy.
Hard Rock Mining
The hard rock mining process acts as a substitute for the use of salt flats for lithium extraction. Lithium is the key constituent of various mineral ores, including spodumene, petalite, and lepidolite that are extracted from pegmatite deposits. The extracted ore is crushed and processed in order to separate the lithium-bearing minerals from the rest of the materials. One of the typical extraction methods is roasting the ore that is concentrated with sulfuric acid and converting lithium into a water-soluble form, which is then purified and converted into lithium carbonate or hydroxide. For instance, open-pit mining has the advantage of not being weather dependent, as well as faster production rates. Yet, it has its downsides, such as more energy consumption and environmental consequences. The industry is working on inventing and implementing sustainable ways to deal with these issues and thereby guarantee a stable lithium industry.
Specific Techniques of Mining lithium
After we have looked at the general approaches to lithium extraction, now we will take a look at the specific techniques used to mine this essential metal.
Thermal Splitting, Mineral Processing Technique
Thermal decomposition is the process of lithium recovery from hard rocks ore. High temperature is applied to break down lithium-bearing minerals. This procedure allows us to isolate lithium from all other elements and, thus, to obtain it for the further processing into lithium hydroxide or lithium carbonate.
The Main Method of Heavy-medium Mineral Processing.
This technique uses the different densities of lithium minerals and waste materials. The heavy medium solution is utilized to suspend the ore that has been crushed. This helps in the separation of lithium-rich minerals by the gravity-based process.
Magnetic Separation
This is also one of the most commonly used methods that is used to separate lithium from ore deposits which have magnetic minerals. Lithium minerals are selectively removed in magnetic separation process, which produces lithium-rich concentrate that is ready for further extraction.
Manual Based Approach of Froth Flotation Technique
Lastly, selection of flotation method for manual basis. For some occasions, hand picking and flotation methods are employed to get lithium minerals from the ore. This method consists of the multi-staged process that begins by the physical separation of the lithium-bearing minerals from the other material (which is called gangue) and then goes to the flotation to further concentrate the product. Also, the increasing demand for lithium is making people look for the most lithium deposits that can be mined with flotation.
Which Lithium Deposits Can Be Mined with Ore Flotation?
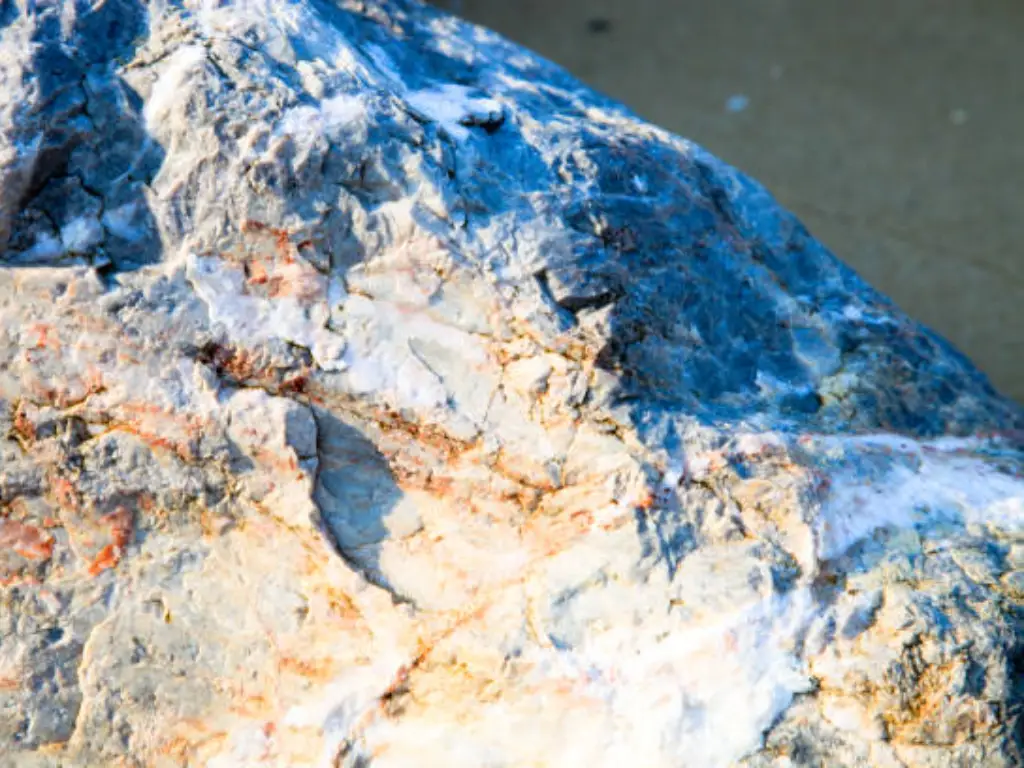
Lithium ore deposits that are commonly mined using the ore flotation process include spodumene, petalite, and lepidolite. These lithium-bearing minerals are often found in pegmatite deposits, which are coarse-grained igneous rocks. In this case study, we will focus on the ore flotation process for a spodumene deposit, as it is the most common lithium ore mineral.
The Process of Ore Flotation for Spodumene
The ore flotation process for spodumene involves several stages, each designed to maximize the recovery and purity of the lithium concentrate. Let’s walk through the process step by step.
Ore Crushing and Grinding
The first stage in the ore flotation process is to crush and grind the spodumene ore which is the raw material for the process. The ore is usually ground by a jaw crusher with the aim of reducing the size of the ore to about 150 mm. The next step is the secondary crushing where cone crusher is used to crush the ore further and reduce the particle size to approximately 25 mm.
Next, the ore is crushed to achieve the particle size of around 150 to 200 microns through the use of a ball mill. The fine grinding element is the most important factor in the liberation of the spodumene crystals from the accompanying gangue minerals, which are mainly quartz and feldspar.
Slurry Conditioning and Preparation
The next step is to grind the ore that has been already crushed to the required size in a grinder and then mix it with water to form a slurry in a conditioning tank. The slurry is then conditioned with chemical reagents comprising of sodium oleate which acts as collector and sodium silicate which is a depressant for the gangue minerals.
The conditioning phase usually occur in a tank with a mechanical agitator to ensure that the reagents are evenly distributed in the slurry. The pH of the slurry is also brought to this range of 8.5 to 9.5 using soda ash or other pH modifiers.
Rough Selection and Cleaner Selection
Following the conditioning process, the slurry is subjected to rough selection by using mechanical flotation cells. During this phase, bubbles are formed in the flotation cell by injecting air into it. These bubbles get stuck to the hydrophobic spodumene particles. Spodumene-rich bubbles ascend to the surface forming a frothy concentrate, which is generally the rough concentrate.
The rough concentrate is further processed via the cleaner selection process which is done through additional flotation stages to remove any remaining gangue minerals. The cleaner flotation cells are run in a slightly different way than the rougher flotation cells, with lower pulp density and more selective reagents, in order to produce a spodumene concentrate of higher purity.
Scavenging and Multiple Cleaning
Therefore, the scavenging stage is the last stage, and the tailings from the cleaner are used in this stage. At this step, further additives are used to the tailings in order to make sure that all the spodumene particles that may have escaped in the previous stages are recovered.
The concentrate from the selection and scavenging stages then goes through different cleaning stages to further increase the purity grade of the spodumene concentrate. These stages normally use column flotation cells, which compared to the conventional cells, provide better separation efficiency due to their increased height and fewer turbulence.
Concentrate Dehydration and Drying
The last spodumene concentrate is typically graded to around 6% Li2O using vacuum filters or thickeners, and then it is dewatered. After the dewatering process, the concentrate is fed into a rotary dryer or a flash dryer until moisture content goes under 1%.
Concentrate Storage and Transportation
The dry spodumene is kept in the sealed bags or bulk containers, so that the moisture absorption and contamination do not occur. Next, the concentrate is transported to chemical processing plants, where it is further processed to produce various lithium chemicals, including lithium carbonate or lithium hydroxide.
Through thoroughly comprehending the spodumene froth flotation process in lithium mines, the owners will be able to adjust their operations and increase the recovery rates and concentrate grades, which in return, will enhance the value of their lithium deposits.
Equipment Category | Equipment | Feed Size Range | Product Size Range | Role |
---|---|---|---|---|
Crushing and Grinding | - Jaw Crusher | 500-1000 mm | 100-300 mm | Primary crushing |
- Cone Crusher | 100-300 mm | 25-100 mm | Secondary crushing | |
Slurry Conditioning and Preparation | - Conditioning Tank | 25-100 mm | 25-100 mm | Mixing ore with water and reagents |
- Mechanical Agitator | 25-100 mm | 25-100 mm | Homogenizing slurry | |
Rough and Sweep Selection | - Flotation Cell | 25-100 mm | 25-100 mm (Tailings) | Separating spodumene from gangue minerals |
- Air Compressor | Supplying air for froth flotation | |||
Featured and Multiple Clears | - Flotation Column | 25-100 mm | 0.1-1 mm | Upgrading spodumene concentrate |
- High Gradient Magnetic Separator (HGMS) | 0.1-1 mm | 0.1-1 mm | Recovering spodumene from flotation tailings | |
Concentrate Dehydration and Drying | - Vacuum Filter | 0.1-1 mm | 10-30% moisture | Dewatering spodumene concentrate |
- Filter Press | 0.1-1 mm | 8-20% moisture | Additional dewatering of concentrate | |
Concentrate Storage and Transportation | - Bulk Containers | <1% moisture | <1% moisture | Storing and shipping concentrate, preventing moisture pickup |
What Challenges and Opportunities of Lithium Mining ?
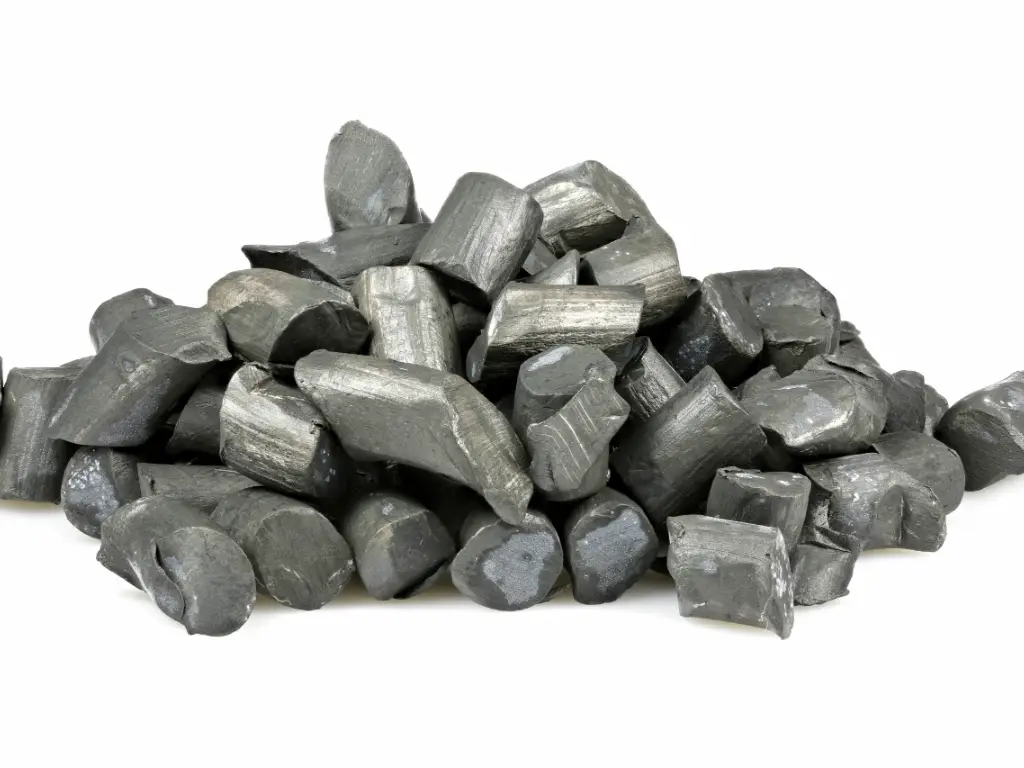
The lithium mining industry is being confronted with the environmental concerns of the extraction methods, and mostly the water usage and carbon emissions. To resolve these problems the industry is employing the innovative technologies and environmentally friendly methods to produce desirable products, for instance, direct lithium extraction and the use of renewable sources of energy. It is also of essence to focus on the enhancement of the efficiency and effectiveness of the extraction and recovery processes. However, the emerging electric vehicles and energy storage systems for renewables sector are the potential drivers of the lithium market. The emergence of alternative lithium sources, e.g., geothermal brines and lithium-rich deposits, could be a way of increasing the global supply. The lithium mining industry can help the planet in going the sustainable way and the technology innovation is the only way to attain the low-carbon future.
Conclusion
Mining of lithium is a vital step in the process of converting to a green and sustainable future. Knowing the processes and techniques involved in lithium extraction is significant and helps to have productive and environmentally friendly operations. With the increasing global need for lithium, the industry should focus on clean energy solutions’ development as well as on reduction of environmental damage associated with the mining process.
All in all, the road of lithium from mine to battery is the example of the interplay of renewable energy, environmental responsibility and technological advancement.